Centrifugal casting method was developed after the turn of the 20th century to meet the need for higher standards.
Spinning molds generate centrifugal force on molten metal to position the metal within a mold. As the molten metal solidifies from the outside in, a casting with dense, close grain structure is created. As a result of close grain structure the centrifugal process offers products with better physical properties than castings made using the static casting method. Proper mold design, mold coatings, mold spinning speeds, pouring speeds, cooling rates and metal chemistry results in castings with higher yields, fewer impurities and greater strength.
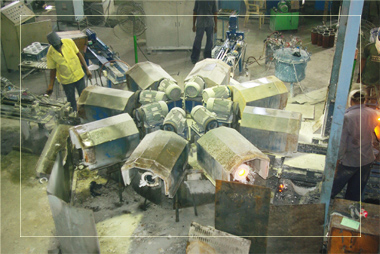
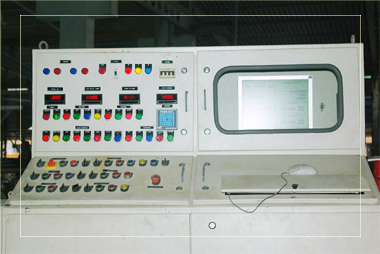